|
|
北京化工大学孙巍教授团队——基于时滞互信息分析的化工过程在线故障诊断 | MDPI Processes |
|
论文标题:Real-Time Industrial Process Fault Diagnosis Based on Time Delayed Mutual Information Analysis(基于时滞互信息分析的工业过程实时故障诊断)
期刊:Processes
作者:Cheng Ji, Fangyuan Ma, Jianhong Wang, Jingde Wang and Wei Sun
发表时间:11 June 2021
DOI:10.3390/pr9061027
微信链接:
https://mp.weixin.qq.com/s?__biz=MzI1MzEzNjgxMQ==&mid=2650011179&idx=1&sn=
14060f0ce942bc1dbfbf2e6ba9d7222a&chksm=f1de4cefc6a9c5f9815c34d0cf7aee7bfe
b1ac41038902c49a5118497f4fd34e26e9b00bc809&token=129349509&lang=zh_CN#rd
期刊链接:
https://www.mdpi.com/journal/processes
原文通讯作者简介

孙巍 教授
北京化工大学
孙巍,北京化工大学教授,承担国家自然科学基金面上项目、973项目、校企合作项目等,涉及非线性过程理论研究、过程监测与智能生产系统开发、医疗数据挖掘和环境生态系统研究。研究领域主要为以数据为基础的过程模式识别、复杂系统的建模和分析等。
文章导读
建立过程变量间的因果关系模型是实现过程故障在线诊断的有效方法,过程知识和专家经验不足以用来建立实时应用的复杂化工过程因果关系模型。而且控制系统的响应会改变变量之间的关系,为化工过程的故障原因分析带来挑战。随着数据采集技术的发展,基于数据的故障诊断方法越来越受到相关领域学者和工程师的关注。
来自北京化工大学的孙巍教授课题组采用时滞互信息分析过程变量关系的实时变化,并应用在化工过程的在线故障诊断中,相关研究成果“Real-Time Industrial Process Fault Diagnosis Based on Time Delayed Mutual Information Analysis” 发表于Processes期刊。
研究内容
本文提出了一种完全基于过程数据信息提取的故障诊断策略,该策略的流程框图如图1所示,该方法首先利用正常工况下的历史数据来计算每对变量之间的互信息值,因为正常工况下,变量都在设定值附近随机波动,大多数变量间的相关性主要由随机噪声产生,因此可以基于正常工况下的历史数据得到变量间互信息值的阈值。一旦检测到过程偏离,利用当前的实时数据计算每一对变量间的互信息值并与阈值进行比较,对超过阈值的变量进行时滞互信息 (TDMI) 分析,从而确定它们之间的因果逻辑,即故障传播路径,并一直追踪到根本原因。该方法被应用于模拟信号和Tennessee Eastman过程。结果表明,该方法能实时捕捉不同运行状态或控制响应下变量相关性的差异,客观地识别故障传播路径,并找出故障根本原因。最后将该方法成功应用于某实际工业过程,证明了该方法在工业应用中的可行性。

图1. 本文提出的故障诊断方法的框架。
研究结果
1. 正常状态和异常状态下变量间的关系变化
将本方法应用于下式中的二元非线性模拟信号 (x,y),其中e1, e2是随机噪声,x和y之间的相关性的时滞为3,并在1500到1700样本设置斜坡故障。
xt=2.8+e1 (1)
yt=x(t−3)∗(1.8−0.5∗x(t−3))+e2
x和y之间的互信息值随时间窗口移动的变化如图2所示。可以发现,当过程平稳运行时,变量x和y之间的互信息值很小,难以获得二者之间的关系。而当引入故障后,二者之间的互信息值显著上升,说明故障在x和y之间传播。基于平稳运行时二者之间的互信息值获取阈值,并在互信息值最先超出阈值的时间窗口计算时滞互信息,结果如图3所示。可以看出,二者在时滞为3的时候互信息值最大,说明二者之间相关性的时滞为3,与设定值相符合。

图2. x和y之间的互信息值随窗口移动的变化。

图3. x和y之间的时滞互信息值。
2. 控制策略影响下的变量因果差异
本方法被用于Tennessee Eastman过程来验证故障诊断效果,由于该过程含有控制回路,变量间的关系在不同的操作状态下受控制响应的影响而发生变化。本方法基于实时数据的信息提取,能够在线捕捉变量间的关系,因此能够正确识别不同操作状态下变量间的关系。
以故障14和故障17为例,基于本方法得到的故障诊断结果分别如图4所示。其中红色节点代表故障的根本原因,蓝色节点代表故障传播过程中的中间变量,绿色代表最终被故障影响的变量。涉及到的变量如表1所示。

图4. (a) 故障14的故障诊断结果; (b) 故障17的故障诊断结果。

表1. 故障14和故障17的变量表。
从两个故障的诊断结果可以看出,反应器冷却水出口温度 (T21) 和反应器冷却水阀门 (V32) 在不同操作状态下的关系出现了反转。故障14引入于反应器冷却水的阀门,导致了反应器冷却水出口温度和反应器温度的变化,从故障的传播路径也可以得到以上结论。而故障17的诊断结果中是反应器冷却水出口温度的变化反而影响了反应器冷却水阀门的变化,这是由于当反应器的温度出现变化时,控制系统响应于反应器冷却水的阀门,改变其开度来使反应器温度恢复正常。常用的基于过程知识或历史数据的分析方法,只能得到变量间固定的关系,针对故障下控制系统响应的情况,就难以得到正确的故障诊断结果。而本方法基于实时数据的信息提取,能够在线的分析变量间关系的变化情况,从而得到更加客观、接近过程本身的故障诊断结果,为工厂操作人员提供指导。
总结
本研究基于时滞互信息分析能够正确获取正常工况和不同故障工况下变量关系的实时变化,并提出了一个完全基于数据信息提取的故障诊断方法,该方法提供了更加客观的故障传播路径与根本原因的识别手段,并可以应用于具有多工况和复杂控制回路的实际工业过程。
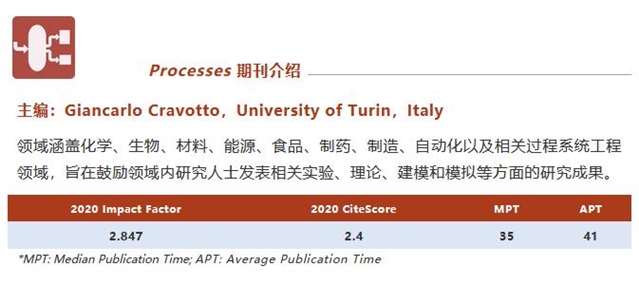
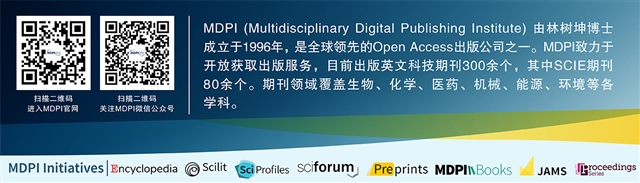
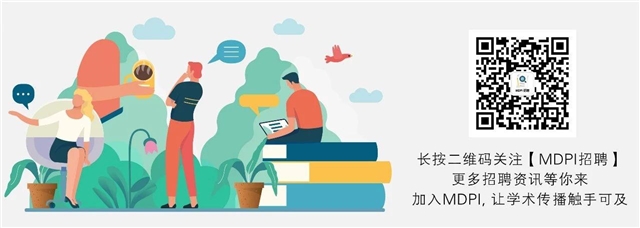
特别声明:本文转载仅仅是出于传播信息的需要,并不意味着代表本网站观点或证实其内容的真实性;如其他媒体、网站或个人从本网站转载使用,须保留本网站注明的“来源”,并自负版权等法律责任;作者如果不希望被转载或者联系转载稿费等事宜,请与我们接洽。